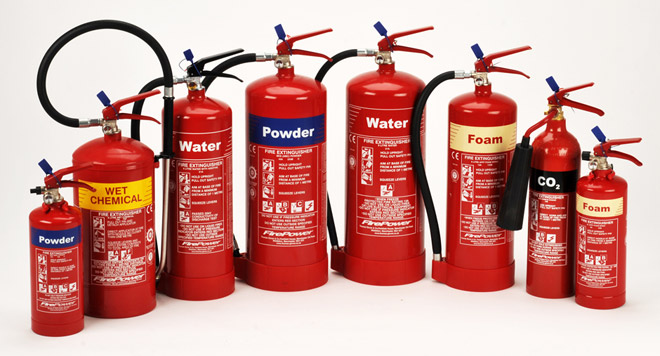
The Occupational Safety & Health Administration (OSHA) recommends annual external maintenance checks of all portable fire extinguishers.
In addition, OSHA has set internal maintenance requirements based on type of extinguisher. See below chart:
Type of Extinguisher |
Test Interval (years) |
Soda acid (soldered brass shells) (until 1/1/82) |
(1) |
Soda acid (stainless steel shell) |
5 |
Cartridge operated water and/or antifreeze |
5 |
Stored pressure water and/or antifreeze |
5 |
Wetting agent |
5 |
Foam (soldered brass shells) (until 1/1/82) |
(1) |
Foam (stainless steel shell) |
5 |
Aqueous Film Forming foam (AFFF) |
5 |
Loaded stream |
5 |
Dry chemical with stainless steel |
5 |
Carbon Dioxide |
5 |
Dry chemical, stored pressure, with mild steel, brazed brass or aluminum shells |
12 |
Dry chemical, cartridge or cylinder operated, with mild steel shells |
12 |
Halon 1211 |
12 |
Halon 1301 |
12 |
Dry powder, cartridge or cylinder operated with mild steel shells |
12 |
Section 1910.157(e)(1) of OSHA standards places the employer with sole responsibility for the inspection, maintenance and testing of all portable fire extinguishers in the workplace.
However, it is recommended that a certified professional or qualified technician perform all maintenance.
Internal Maintenance Basics
When technicians perform an internal inspection, the process generally includes:
- Examining the overall condition of the exterior of the unit
- Discharging the extinguishers into an agent reclaiming system
- * Removing and disassembling the valve
- Inspecting and evaluating the internal components, replacing any that are worn, damaged or corroded
- Reassembling the valve and testing the discharge lever
- Inspecting the empty cylinder internally for corrosion or foreign matter
- Refilling the cylinder with the proper amount of chemical agent
- Installing verification collar and reinstalling the valve assembly
- Re-pressurizing the extinguisher for the specified operating pressure
- Performing a leak check
- Reattaching the hose and installing proper safety labels and record tags
Renegade Dust Control
During step 3*, removing and disassembling the valve, a plume of dust and particulate that was residing in the internal chambers of the extinguisher is generated and enters the operators breathing zone.
The plume from a single extinguisher may be a nuisance, but in facilities where hundreds of extinguishers are inspected each month, dust will accumulate and may become hazardous.
When surfaces or machinery have an accumulation of dust there is a higher risk of machine failure. A more serious side effect of dust is inhalation which can result in a plethora of respiratory-related illnesses.
In order to maintain a clean, air-friendly workspace, a dust containment system is a great solution.
A Cleanable, Cost-Saving Solution
We recently created this cleanable, source-capture configuration for a customer who performs routine fire extinguisher maintenance.
The customer previously used another company’s downdraft table that would exhaust captured particulate outdoors.
However, they were moving to a new building which required a ductless system.
Instead of providing the customer with one of our own ductless downdraft tables, our Technical Applications Specialists agreed that by doing so, the amount of captured dust would quickly saturate a HEPA filter, requiring costly annual filter replacements for the customer.
As a solution, we recommended a semi-custom 40-inch wide ductless containment hood paired with a Model 300 Roundaire, synced with a flame-retardant flex hose.
In this configuration, the hood provides a contained workspace while the Model 300 Roundaire utilizes 725 Cubic Feet per Minute (CFM) of airflow to pull the dust and particulate away from the operators breathing zone and into a MERV16-rated Micro-Pleat Series 2 filter. Cleaned, filtered air is released back into the surrounding work area.
The cleanable filter will save the operator thousands in annual filter replacement costs.
For more information
If you work with powders and seek a containment solution, contact Sentry Air Systems at 800.799.4609, visit our website, email sales@sentryair.comor fill out the feedback form below.
Resources
1. SAS – Model 300 Roundaire Demonstration Video [Welding Application]
2. OSHA Standards on Fire Protection – Portable Fire Extinguishers
3. Photo source – Image of lined up fire extinguishers
4. Step-by-Step Guide to performing internal maintenance of a fire extinguisher