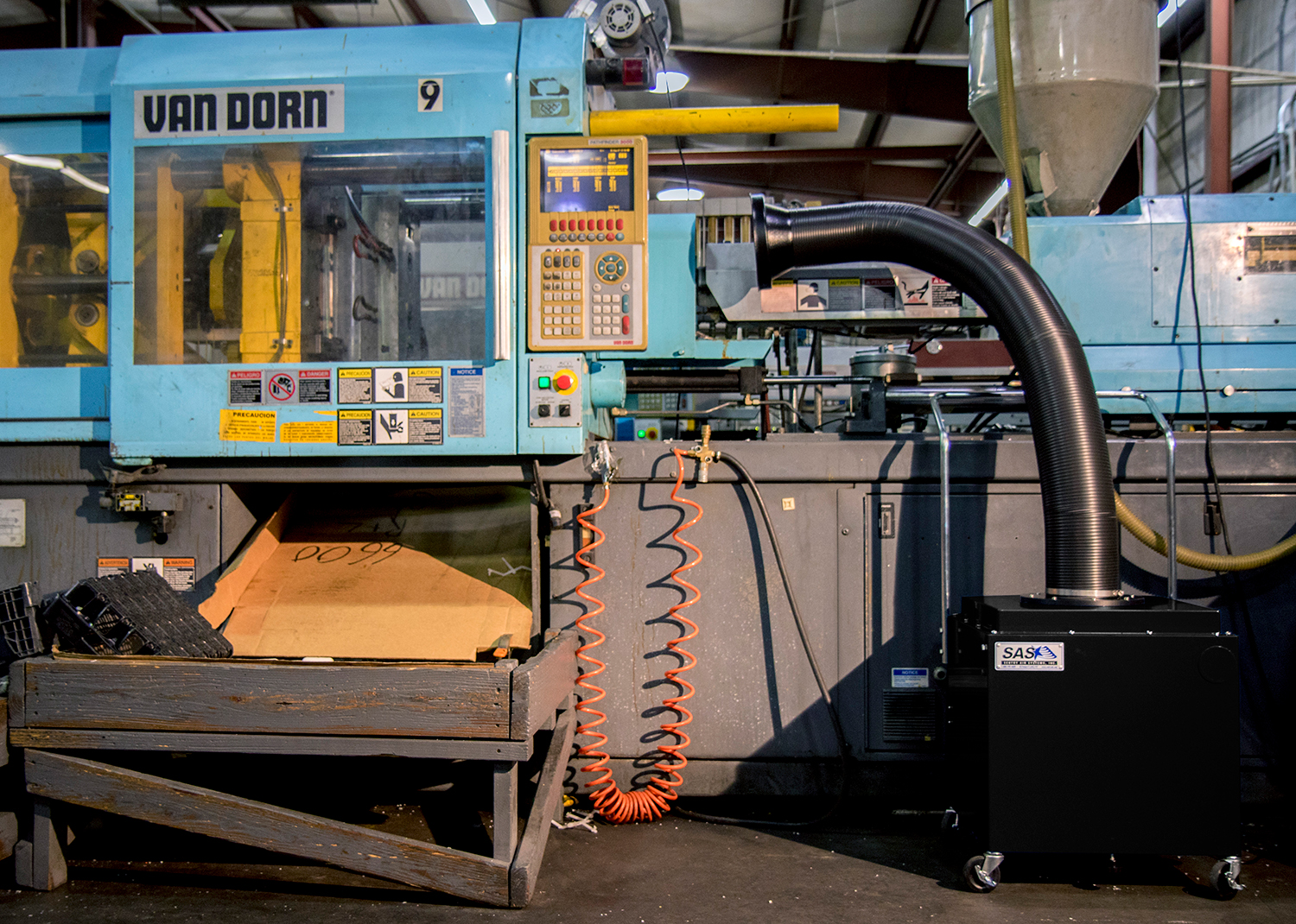
The Model 400 Portable Fume Extractor captures plastic fumes at the source to help remove most from the airflow.
According to the Plastics Industry Trade Association, in 2011 the U.S. plastics industry accounted for $380.4 billion in annual shipments and directly employed almost 900,000 people in over 16,200 facilities. With such a huge economical impact, it is vital to protect the respiratory health of the plastics industry workforce.
The basics of plastics
There are two main categories in plastics processing: Thermoplastic and Thermoset materials.
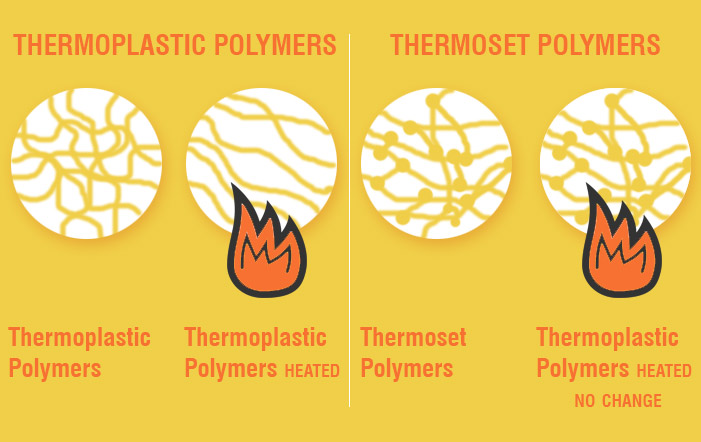
The difference between Thermoplastic and Thermoset (Source)
Thermoplastics
Thermoplastics have the ability to re-melt and re-form which is why a majority of plastic products are made from these resins.
Common thermoplastic resins include:
• Polyethylene ― PE
• Polyvinyl Chloride ― PVC
• Polypropylene ― PP
• Polystyrene ― PS
• Polyethlene Terephthalate ― PET
• Acrylonitrile-butadiene-styrene ― ABS
• Styrene-Acrylonitrile ― SA
• Acrylic ― PMMA
• Polyamide ― PA (Nylon)
• Styrene-Acrylonitrile ― SAN
• Polycarbonate ― PC
During the injection molding process, these resins are melted, injected into molds, rapidly cooled and released all within a matter of minutes; all the while emitting hazardous fumes and vapors that pose health risks if inhaled.
Thermoset
Thermoset materials undergo chemical reactions to melt, shape, cure and harden into objects. Due to its chemical structure, thermosets have a higher degree of rigidity and tend to outperform other materials in regards to mechanical properties, chemical resistance, stability and durability. However, once cured, thermosets are never able to be re-softened or reshaped
Plastic Injection Molding Process
The below graphic illustrates the basic injection molding process. This blog focuses on three process areas of respiratory concern: Purging & Maintenance; Heating & Melting; Cooling & Removal
Purging & Maintenance
Before a new mold can be injected, the residual resins must be removed from the machine. This process requires very high heat to melt resins and purging agents in order to press them through the machine. As a result, smoke and fumes emit and enter the operator’s breathing zone.
Heating & Melting
Similar to the purging process, resin pellets are heated at high temperatures until they reach their melting point. At which time, the melted resins are pressed through a rotating screw and into the mold. This process also emits hazardous smoke, fumes and gases that may have adverse health effects if inhaled. The below table shows the respiratory hazards and side effects one may encounter when working with plastic materials.
Common Plastic Material Respiratory Hazards & Side Effects
Plastic | Constituents in Fume | Exposure Limits | Side Effects |
PVC | Hydrogen chloride | NIOSH REL: (C) 5 ppm (7 mg/m3) OSHA PEL: C 5 ppm (7 mg/m3) |
Irritation to nose, throat, larynx; Cough, choking; Dermatitis; Laryngeal spasm and pulmonary edema found in animals |
Fire-retardant ABS | Styrene | NIOSH TWA: 50 ppm (215 mg/m3) OSHA TWA: 100 ppm |
Irritation to eyes, nose, respiratory system; headache, weakness, exhaustion, dizziness, confusion, drowsiness, unsteady gait; narcosis; defatting dermatitis; possible liver injury; reproductive effects |
Phenol | NIOSH TWA: 5 ppm OSHA TWA: 5 ppm |
Irritation to eyes, nose, throat; anorexia, weight loss; weakness, exhaustion, muscle ache, pain; dark urine; cyanosis; liver, kidney damage; skin burns; dermatitis; ochronosis; tremor, convulsions, twitching | |
Butadiene | OSHA TWA: 1 ppm | Irritation to eyes, nose, throat; drowsiness, dizziness; teratogenic, reproductive effects; potential occupational carcinogen | |
Polypropylene | Formaldehyde | NIOSH TWA: 0.016 ppm, (C) 0.1 ppm (15-minute) OSHA TWA: 0.75 ppm, ST 2 ppm |
Irritation to eyes, nose, throat, respiratory system; lacrimation (discharge of tears); cough; wheezing; potential occupational carcinogen |
Acrolein | NIOSH TWA: 0.1 ppm (0.25 mg/m3), ST 0.3 ppm (0.8 mg/m3) OSHA TWA: 0.1 ppm (0.25 mg/m3) |
Irritation to eyes, skin, mucous membrane; decreased pulmonary function; delayed pulmonary edema; chronic resp. disease | |
Acetone | NIOSH TWA: 250 ppm (590 mg/m3) OSHA TWA: 1000 ppm (2400 mg/m3) |
Irritation to eyes, nose, throat; headache, dizziness, central nervous system depression; dermatitis | |
Acetals | Formaldehyde | NIOSH TWA: 0.016 ppm, (C) 0.1 ppm (15-minute) OSHA TWA: 0.75 ppm, ST 2 ppm |
Same as above |
Polyethylene (low density) | Butane | NIOSH TWA: 800 ppm | Drowsiness, narcosis, asphyxia |
Polystyrene | Styrene | NIOSH TWA: 50 ppm (215 mg/m3) OSHA TWA: 100 ppm |
Same as above |
Legend: C = Ceiling, TWA= Total Weighted Average over 8 hour work shift, PEL= Permissible Exposure Limit, REL= Recommended Exposure Limit.
Cooling & Removal
During the final stages, curing occurs by quickly cooling the mold. This coolant tends to send renegade mist into the air, compromising the ambient air quality in the workspace. Lastly, when the mold is released from the machine, tiny release agents and particles may emit and enter the operator’s breathing zone.
Engineering Controls for Plastic Injection Molding
In order to recommend the most appropriate fume extraction system, Sentry Air technical applications specialists consider the size of the molds being created and the types of fumes that must be captured.
Model 300 Portable Fume Extractor
For a majority of injection molding applications, we recommend our Model 300 Portable Floor Sentry (SS-300-PFS) with a filter combination of HEPA and 10lbs of activated carbon. The Model 300 utilizes up to 350 CFM of airflow to pull harmful plastic fumes away from the operator’s breathing zone and directly into the filter chamber. The HEPA filter is 99.97% efficient on particles 0.3 microns and larger while the activated carbon filter utilizes thousands of carbon granules to capture renegade odors from volatile organic compounds typically found in plastics fume.
Model 400 Portable Fume Extractor
For applications requiring a greater amount of smoke capture, we recommend our Model 400 Portable Floor Sentry (SS-400-PFS) with a filter combination of HEPA and 22lbs of activated carbon. The Model 400 offers heavy-duty airflow up to 700 CFM. Both the Model 300 and 400 come equipped with heavy-duty casters and portability handle, allowing easy placement around the injection molding machine.
Ambient Air Filtration – Model 2000
And for removing ambient or renegade fumes from the greater work area, a Model 2000 Free Hanging Ambient Room Air Cleaner is recommended. This system provides a secondary engineering control offering up to 2,000 CFM. The Model 2000 Ambient Air Cleaner can be mounted on a wall, on a cart, or hung from the ceiling.
Help Reduce Respiratory Hazards of Plastic Injection Molding in your Facility by Contacting Sentry Air Today!
If your business is seeking a solution to fume control for plastics processing, or if you want more information about chemical fume control, contact us today.
Call us today to talk to an application specialist – 1.800.799.4609
Resources
• Chemical Exposures of Women Workers in the Plastics Industry with particulate Reference to Breast Cancer and Reproductive Hazards
• Health and Safety Executive – Controlling fumes during plastics processing
• Comparison of Thermoset Versus Thermoplastic Materials
• The Plastics Industry Trade Association