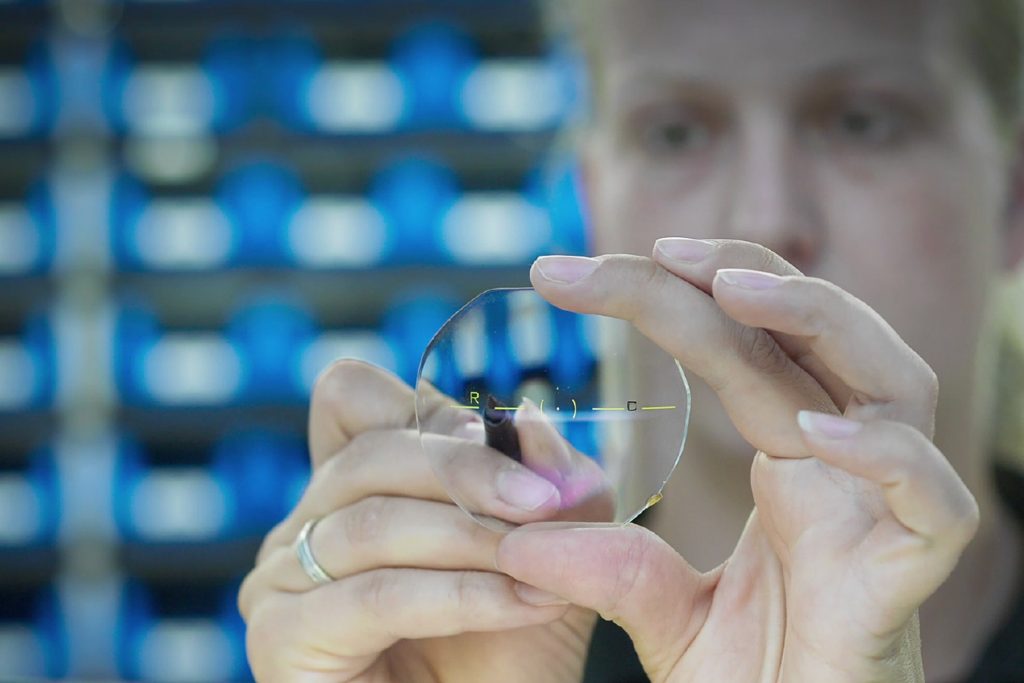
Technician inspecting an lens and marking the optical center (Source)
Reflective surfaces have been used to magnify and enhance vision since the early 1200s with the discovery of the magnifying glass made of quartz and beryl lenses1. Glasses were introduced to the general public by Alessandro di Spina. Due to high demand, quartz and beryl lenses were quickly replaced with glass. Modern day eyeglass lens production uses high quality polycarbonate making glasses lighter and less easily breakable2.
What are the steps for eyeglass lens production?
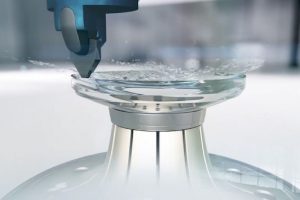
CNC machine grinding a lens (Source)
Grinding
Based on a prescription, the technician chooses the appropriate semi-finished lens that already has the optical power finished on the front side3. The finished side is covered in plastic to protect the surface while the other side is grinded3. A block or hold for the machine is created using molten metal on the covered side. This block allows the machine to grip the lens during processing. The exact measurements for the prescription are input and the lens in placed in a 5 axis CNC machine to be grinded down using tens of thousands machining points with a natural diamond3.
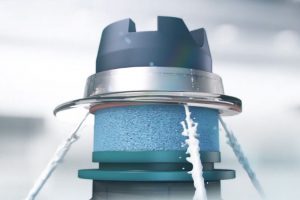
Machine polishing a lens with polishing compound (Source)
Polishing
After grinding, the lens still has rough concentric circles and must be polished with abrasive sand paper and water, at a consistent temperature of 19 ° C, to smooth the lens and maintain the correct shape4. The lens is then polished again using sandpaper with a polishing compound of aluminum oxide, water and polymers to complete the smooth surface on the back of the lens4. The block and plastic covering are removed from the lens and then the lens is cleaned using a 15 step chemical bath4. The lens is then inspected for accuracy by hand by technicians.
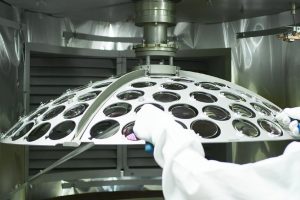
Operator placing lens in an oven to remove impurities and to add anti-glare coating (Source)
Anti-Glare Coating
In a cleanroom setting, the lenses are placed in an oven to remove impurities and an anti-glare coating is applied to both sides5. Anti-glare coating utilizes metals such as silicon oxide, titanium oxide or zirconium oxide to reduce the amount of glare on a lens4. A cleanroom is required for this step to protect the lens from particulate and other contaminants to ensure a high quality coating.
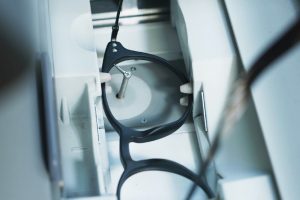
Machine taking measurements of the frames before cutting the lenses to fit (Source)
Finishing
After coating, the lenses are ready to be cut down to fit the size of the frames. A robotic cutter measures the frames and then makes the cuts to the edges of the lenses to fit the specifications. Technicians conduct a final inspection to double check the accuracy of the lenses compared to the prescription.
Particulate & Fume Exposure in Eyeglass Lens Production
During eyeglass lens production, there are several particulates or fumes that could be inhaled by operators causing health effects. Polycarbonate or plastic dust disperses into the air and collects within the grinding machine during manufacturing processes. Even in an enclosed machine, the operator may be exposed to plastic dust when cleaning the machine or switching to a different lens. During the polishing step of eyeglass lens production, polishing compounds and water combines with plastic dust forming a mist which could pose health effects. Both plastic dust and mist inhalation could be dangerous to the operator’s health. Plastic dust contains microparticles of plastic which could become embedded deep in the lungs. The plastic microparticles could expose the lungs to the chemicals in the plastic or cause infections, coughing, lung disease, or lung function limitations6. Sometimes the particles simply pass through the body without causing any effects. The full effects of breathing plastic microparticles are not clear but both indoor and outdoor air contains plastic dust. Particularly industrial or commercial areas contain more plastic microparticles concentrations in the air. Plastic dust exposure may also cause eye or skin irritation7.
The metals or chemicals used for the anti-glare coating step of eyeglass lens production can cause respiratory irritation after inhalation. Silicon dioxide is not listed by OSHA but could be harmful to the lungs8. Titanium oxide exposure has been shown to cause nausea, dyspnea, and irritation to the respiratory system9. Inhalation of titanium oxide in rare cases has caused metal fume fever with fever like symptoms9. Zirconium oxide exposure should be reduced as it is a respiratory irritant as well10. The cleanroom requirements of the anti-glare room would require plastic dust and other particles to be minimized to ensure high quality production.
Particulate & Fume Exposure in Eyeglass Lens Production
A wide variety of particulate and fume control solutions would prevent operators from exposure to plastic dust and chemical fumes from anti-glare coating. The best suited solution would depend on the setup and size of the eyeglass lens production facility. All of Sentry Air Systems fume extractors and air purification systems use a fan to pull the hazard away from the operator and filter out the particulate and/or fume releasing the air back into the surrounding room. These systems do not require expensive external ductwork or makeup air.
Mist Collectors
SS-300-MIST
For large CNC grinders and polishers used in eyeglass lens production, the Model 300 mist collector would provide a source capture solution to minimize plastic dust and polishing mist. The Model 300 mist collector mounts directly on the machinery to filter out particulates and mist produced from the manufacturing process. This filtration system utilizes a HEPA filter with up to 99.97% efficiency on particles as small as 0.3 microns. Other sizes of mist collectors are available from 80 CFM up to 950 CFM. Sentry Air also offers an ambient air mist collector. The ambient air mist collector hands nearby and filters the air of harmful mist. The ambient air mist collector would be great to use in conjunction with a source capture mist collector to ensure optimal high quality filtration.
Portable Fume Extractor
SS-300-PFS
The Model 300 portable fume extractor can be used to capture particulate at the source for open CNC grinder units used for eyeglass lens production. This lightweight unit comes with heavy duty casters allowing the unit to be moved for multiple purposes. The Model 300 portable fume extractor captures particulates with a self-supportive flexible hose which can easily be adjusted. With HEPA filtration, this system filters the air removing the hazard from the operator’s breathing zone.
In applications with heavy loading, Sentry Air has high efficiency cleanable filtration media including the Rugged Air and the Model 500 Heavy Duty Industrial Fume Extractor. The RuggedAir model is best suited for smaller machinery or handling areas with heavy duty usage. The cleanable filters provide an added benefit by simply cleaning the filter when full instead of replacing it. The Model 500 Heavy Duty Industrial Fume Extractor works well for large machinery with heavy duty particulate production. This unit can also be equipped with dual arms to allow multiple machinery to be filtered with one system.
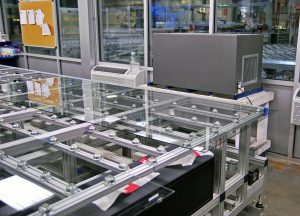
Model 2000 Ambient Air Cleaner mounted on a shelf for particulate extraction.
Free Hanging Ambient Air Cleaners
SS-2000-FH
Coupled with a source capture device, the ambient air cleaners provide extra protection to clean the workspace air for worker safety during eyeglass lens production. The Model 2000 would hang or be mounted on top of a table in a large lens manufacturing facility and provide protection when the primary control extractor may not be in use such as during machine cleaning or when switching orders. This hanging air cleaner would also help in the anti-glare coating application room to instill a cleanroom environment and protect against chemical fume exposure. This system utilizes a HEPA filter and a carbon filter to remove fumes and particulates from the air. For mist collection, the Model 2000 Ambient Mist Collector would provide added support to ensure a healthy breathing zone for workers.
Portable Room Air Cleaners
SS-300-PRAC
Smaller air cleaner devices such as the Model 300, can be placed on the floor, a benchtop, or mounted on a stand to clean ambient air. These air cleaners would be best suited for smaller workspaces and for inspection tables to ensure removal of particulates while the worker handles the lenses. The Model 300 air cleaner uses a HEPA filter for particulate control or an activated carbon filter for chemical fume extraction. It could also be utilized in the anti-glare coating application room complete with an activated carbon filter to protect against chemical fumes.
Ductless Fume Hoods
AirHawk30
For small polishing, grinding and most edging machines, the entire system can be contained within a ductless fume hood for particulate control. The Sentry Airhawk 30” ductless fume hood uses a HEPA or activated carbon filter to clean the air before releasing it back into the surrounding room. This style of ductless fume hood comes standard with an adjustable fan and light allowing the operator to make adjustments. The Sentry AirHawk is available in 30”, 40” and 50” accommodating for your size of equipment.
If you have an application that needs plastic particulate removal or other chemical fume extraction similar to eyeglass lenses production, please contact our sales team:
sales@sentryair.com • 1-800-799-4609 • www.sentryair.com
Sources
1. “Eyeglass Lens.” How Products are Made, http://www.madehow.com/Volume-1/Eyeglass-Lens.html.
2. “What are Glasses Lenses Made of?” Eyebuydirect, 23 March 2018. https://www.eyebuydirect.com/blog/what-are-glasses-lenses-made-of/.
3. “How are Spectacle Lenses Manufactured?” Zeiss, 28 March 2018. https://www.zeiss.com/vision-care/int/better-vision/understanding-vision/how-are-spectacle-lenses-manufactured.html.
4. “Eyeglass Lenses, Granite, Potato Chips, Microprocessors.” How It’s Made. Discovery Channel. 17 Aug 2005. Television. https://www.youtube.com/watch?v=BCH1SEYbrVA.
5. (2012, Nov 15). How Eyeglass Lenses are Made. Clarkson Eyecare Media. https://www.youtube.com/watch?v=RYrG3G8nhhA.
6. Uffelen, Carina. “How Damaging is Breathing Microplastics?” Plastic Soup Foundation. 23 Mar 2018. https://www.plasticsoupfoundation.org/en/2018/03/how-damaging-is-breathing-in-microplastics/.
7. “Material Safety Data Sheet: Polycarbonate.” ACP NOXTAT. http://www.noxtat.com/wp-content/uploads/2011/04/MSDS-SheetPC_TEC_2000_TEC_FUSION_2004.pdf.
8. “Silicon Oxide Safety Data Sheet.” ESPI Metals. Nov 2015. http://www.espimetals.com/index.php/msds/244-silicon-oxide-sio.
9. Otani N, Ishimatsu S, Mochizuki T. “Acute Poisiong by Titanium Dixoide: Inhalation may cause Metal Fume Fever.” Am J Emerg Med. Jun 2008. https://www.ncbi.nlm.nih.gov/pubmed/18534293.
10. “Zirconium Oxide Safety Data Sheet.” ESPI Metals. Jan 2007. http://www.espimetals.com/index.php/msds/315-zirconium-oxide.